The feed pellet extruder machine is commonly used in the fish feed production line. The whole line mainly processes crushed grains, straw, husk, fish meal, meat meal, a bone meal into feed pellets to feed aquatic animals and pets. The whole fish feed pellet production line includes two types, dry process and wet process. Both lines output feed pellets with high automation. According to different raw materials and capacity demands, we provide different models of machines for customers’ choice.
What are the applicable scopes of fish feed production lines?
The whole fish feed production line is widely applied to the aquaculture industry and pet food processing industry. And this is fully in line with the modernization of the agricultural machinery production line. In recent years, this production line has been favored by the majority of consumers from America, Nigeria, Ghana, Peru, Tanzania, Pakistan, Colombia, Niger, Angola, Malaysia, etc.
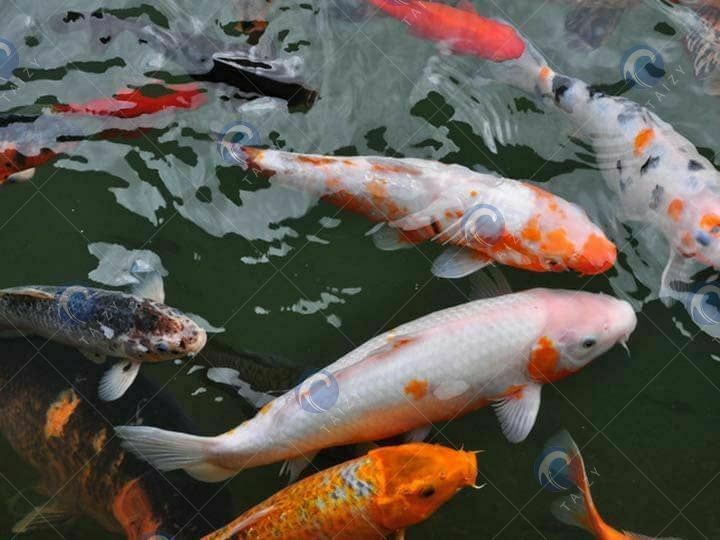
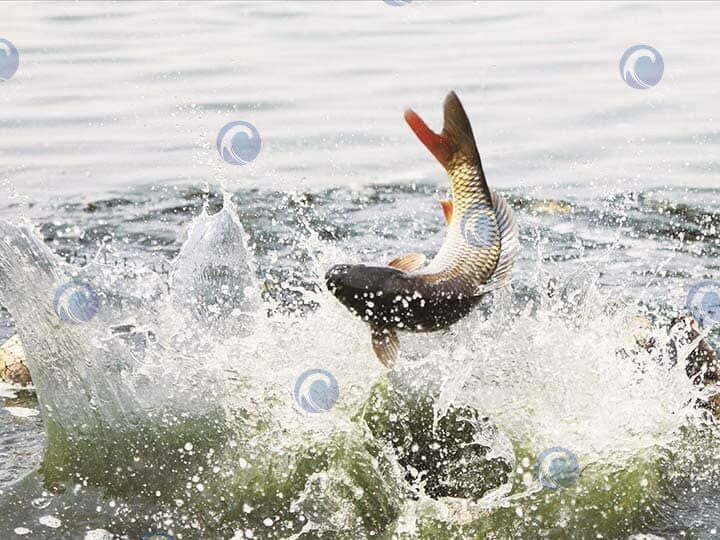
Dry process feed extruder production line
Technological process
Raw material crusher→ mixer→ screw conveyor→ extruder→ pneumatic conveyor→ dryer→ bucket conveyor→ counter flow cooler→ roller sprayer→ bucket conveyor→ finished product bin→ packing machine
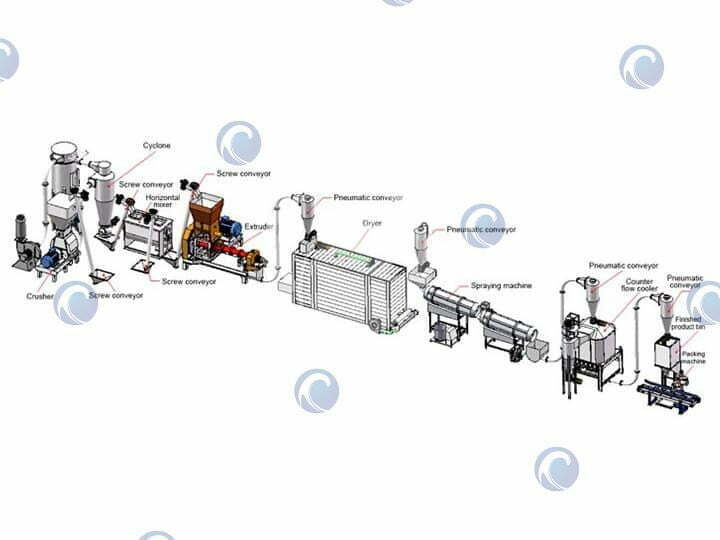
Brief introduction
The crusher machine crushes the raw material, hammer mill machine is always a good choice. The screw conveyor transferred the crushed material into the mixer. After equal blending, the material goes into the fish food making machine. The extruder squeezes and outputs pellets into the pneumatic conveyor, and then the pellets are transferred to the dryer.
The mesh belt dryer dries pellets layer by layer and then goes out into the counterflow cooler. The pellets come from the cooler, then go into the spraying machine, and it sprays pellets evenly. Some grease will increase the palatability and allure of pellets. The bucket conveyor will send the pellets to the finished product bin, to some consumers, the fish feed production line is finished now. But customers can also choose to add one packing machine to package those pellets into bags, which can be sold easily.
Wet process feed extruder production line
Technological process
Raw material crusher→ mixer→ screw conveyor→ conditioning apparatus→ boiler→ fish feed extruder→ pneumatic conveyor→ dryer→ bucket conveyor→ counter flow cooler→ roller sprayer→ bucket conveyor→ finished product bin→ packing machine
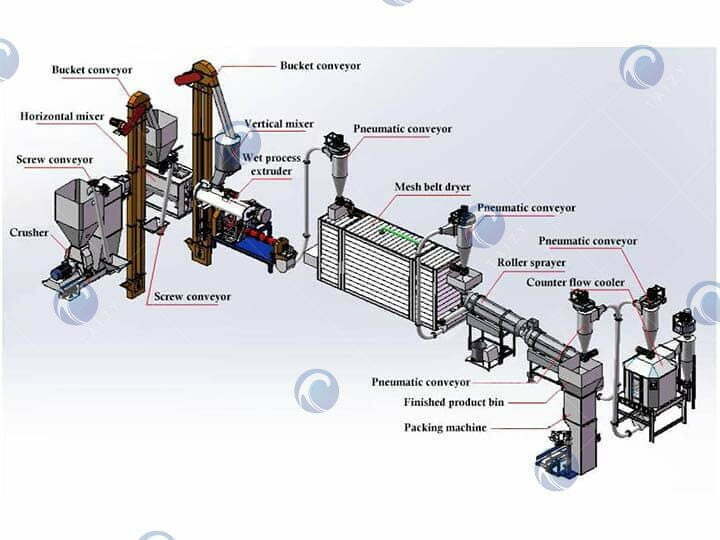
Brief introduction
The raw material after crushed by the crusher, then transferred by a screw conveyor into the mixer. After being equally stirred and mixed, the material goes into the conditioning apparatus. The conditioning apparatus connects to the boiler, which turns material into steam, and then the conveyor transfers material into the pet food extruder. This step is the main point that’s different from the dry process production line.
The extruder outputs pellets into the pneumatic conveyor, and then the pellets go to the dryer. The mesh belt dryer dries pellets, then pellets go out into the counterflow cooler. After cooling, the pellets go into the roller sprayer and get grease sprayed evenly. The bucket conveyor will send the pellets to the finished product bin, and finally, the packing machine packages pellets into bags.
Difference between dry and wet process feed extruder production line
The dry process is to crush the raw material and mix it well, then expand it into pellets directly.
The wet process needs a steam boiler, and the extruder also needs to be equipped with a conditioning apparatus, which connects with the boiler through a pipe. After crushing and mixing, the advanced conditioning apparatus and steam can fully pre-mature the pellets, and then the extruder can squeeze the material into pellets.
Compared to the same power of the two types, the wet process machine output is higher, and the material will be slightly delicate. However, the wet process needs a steam boiler, and the production process is relatively intricate.
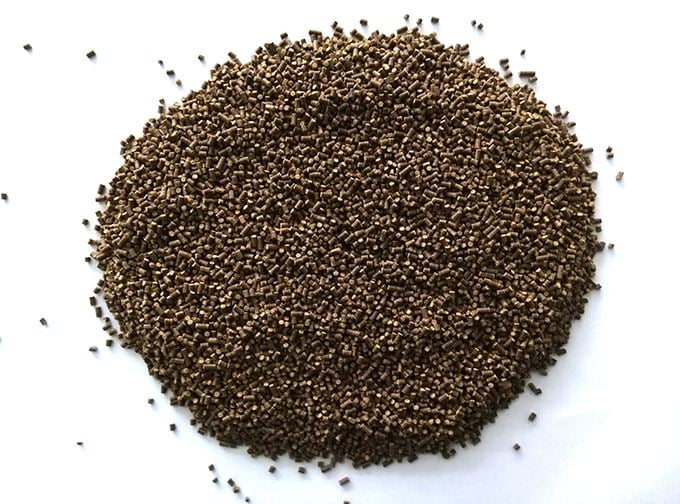
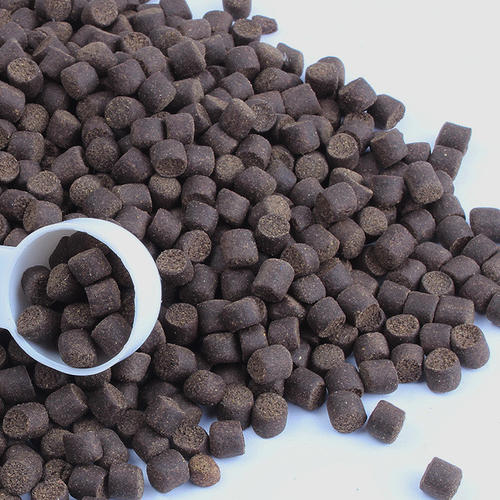
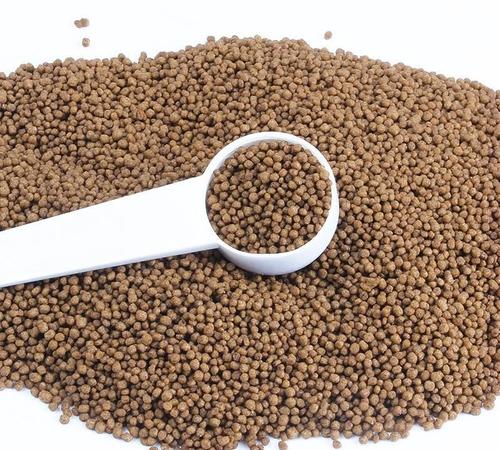
Main machines introduction
Crusher
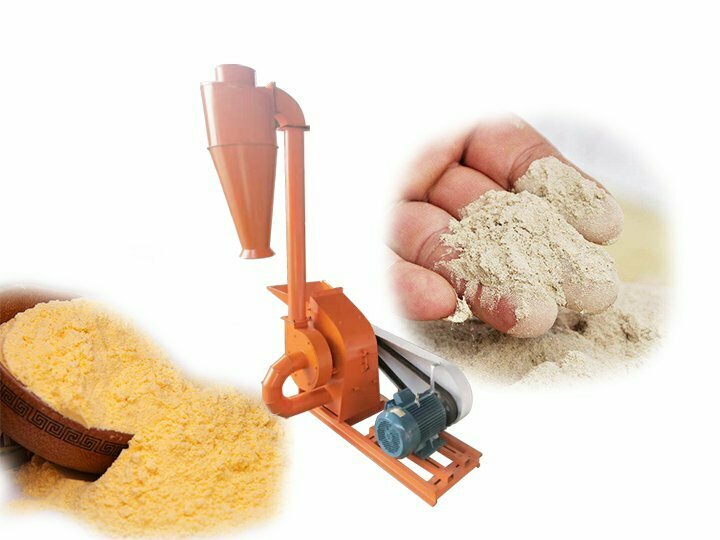
The crusher part of the feed pellet production line mainly consists of two machines, the grain grinder machine and the cyclone. We provide a hammer mill machine like a crusher, which uses hammers and sieves to output fine powder of raw material. Cyclone collects the dust and reduces the internal pressure of the crusher, then increases the capacity.
Specification | 9FQ-320 | 9FQ-360 | 9FQ-500 |
With cyclone or not | No | Yes | Yes |
Power | 2.2kw electric motor | 3kw electric motor170F gasoline engine6HP diesel engine | 11kw electric motor15HP diesel engine |
Capacity | 300-500kg/H | 300-400kg/H | 500-600kg/H |
Size | 830*635*968 mm | 800*650*720mm | 2000*850*2200mm |
Weight | 65kg | 60kg | 150kg |
Qty of hammer | 16 pcs | 18 pcs | 24pcs |
Mixer
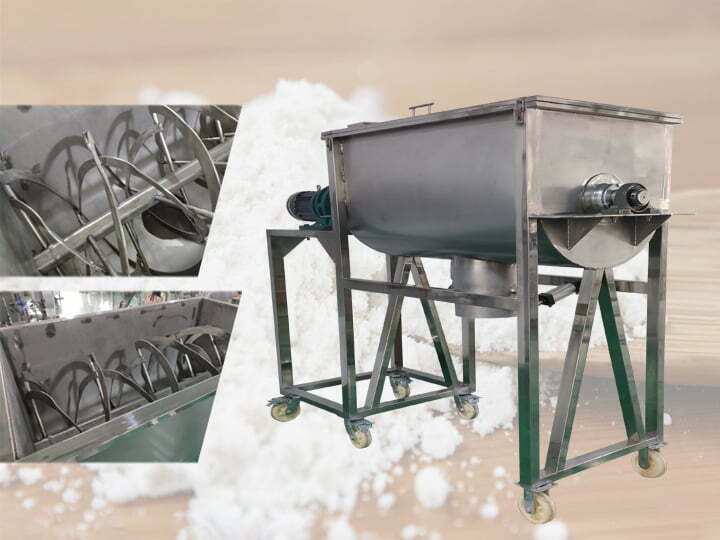
According to the formula and ingredient standards, the required raw materials are accurately weighed. Then the mixer processes weighed raw materials into semi-finished products with the mixing uniformity up to the technical requirements.
Name | Horizontal mixer |
Volume | 1.5cbm |
Wall thickness | 5mm |
Reducer power | 11KW/380V-50Hz |
Rotate speed | 18r/min |
Discharging way | Cylinder open form |
Machine size | 2100*1400*2000mm |
Bucket size | 1700*1200*1400mm |
Material | Parts in contact with materials are made of stainless steel, the rest parts are carbon steel. |
Conveyor

The conveyor includes a screw conveyor, a pneumatic conveyor, and a bucket conveyor. The conveyor is an important machine to improve the automation of the production line.
Name | Screw conveyor |
Voltage | 380V/50HZ |
Installation power | 0.75KW |
Real consumption power | 0.75KW |
Capacity | 80-300Kg/time |
Size | 1.5×0.7×2.5m |
Extruder
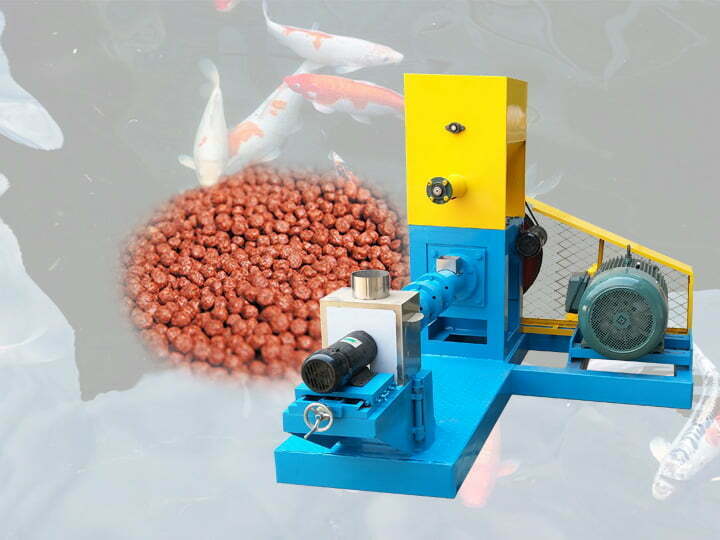
It’s the main machine of the whole fish feed production line. It decides the capacity of the line and variety of model,s mainly distinguished by output. The shape and figure are adjustable by changing the molds of the extruder.
Model | Capacity(t/H) | Main Engine Power(kw) | Feeding Power (kw) | Screw Diameter (mm) | Cutting Power (kw) |
DGP40 | 0.04-0.05 | 5.5-7.5kw12HP diesel engine | 0.4 | 40 | 0.4 |
DGP50 | 0.06-0.08 | 11 | 0.4 | 50 | 0.4 |
DGP60 | 0.10-0.12 | 15 | 0.4 | 60 | 0.4 |
DGP70 | 0.18-0.20 | 18.5 | 0.4 | 70 | 0.4 |
DGP80 | 0.25-0.30 | 22/27 | 0.4 | 80 | 0.55 |
DGP90 | 0.4 | 30 | 0.75 | 90 | 1.5 |
DGP100 | 0.5 | 37 | 0.75 | 100 | 1.5 |
DGP120 | 0.60-0.70 | 55 | 1.1 | 120 | 1.5 |
DGP135 | 0.75-0.80 | 75 | 0.75 | 133 | 1.5 |
DGP160 | 1.0-1.2 | 90 | 1.5 | 160 | 2.2 |
DGP200 | 1.8-2.0 | 132 | 2.2 | 200 | 2.2 |
Dryer
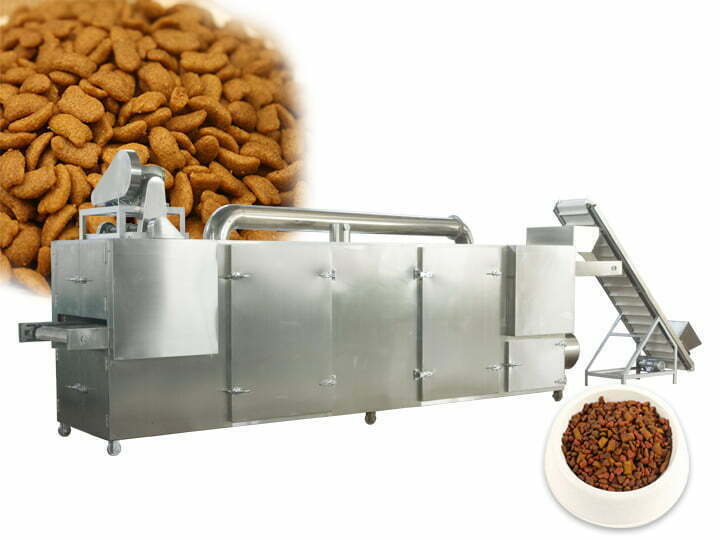
The fish feed production line adopts a mesh belt dryer machine. It dries pellets layer by layer evenly and can remove the moisture content of feed pellets. The dryer can increase the storage time of pellets. Besides, the conveyor transfers the pellet into the dryer automatically, which saves a lot of human labor.
Model | DLD3-II |
Layers | 3 |
Voltage | 380V/50HZ |
Installed Power | 45KW |
Power Consumption | 30KW |
Capacity | 100-150Kg/h |
Size | 5.2×1.2×1.6m |
Counter flow cooler
It is the most advanced cooling technology for pellet feed in the world, mainly for the cooling of high-temperature feed pellets after pelletization. The feed pellets through the cooler are not easy to deteriorate and can be preserved for a long time. It’s a necessary machine in the fish feed production line.
Name | Cooling conveyor |
Voltage | 380V/50HZ |
Installation power | 0.75KW |
Quantity of fan | 4pcs |
Power of fan | 0.15kg/pcs |
Capacity | 100-300Kg/h |
Size | 5.0×0.4×0.4m |
Oil spraying machine
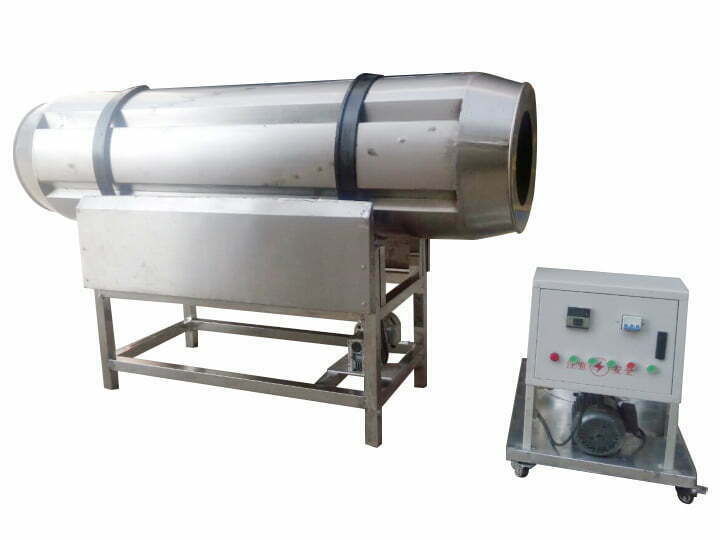
oil spraying machine
You can spray grease onto the pellets. The pellets increase the palatability and attraction, which makes the feed pellet much easier for animals to eat.
Main machine power | 0.75kw |
Oil pump power | 0.37kw |
Capacity | 300-400kg/H |
Size | 2450*650*1450mm |
Weight | 190kg |
Packaging machine

This is optional equipment for the fish feed production line. Various models are mainly distinguished by the weight per bag. We provide many choices for customers who want to sell the pellets directly after production.
Back Seal | 3 Side Seal | 4 Side Seal | |
Packing Speed | 32-72 bags/min 50-100 bags/min | 20-80 bag/min | 24-60 bags/min 50-100 bags/min |
Bag Length | 30-180mm | 30-150mm | 50-150mm |
Bag Width | 25-145mm | 25-145mm | 25-145mm |
Packing Range | 22-220ml | 2-20ml | 22-100ml |
Power | 1.8 KW | 1.8 KW | 2.2KW |
Weight | 250 KG | 250 KG | 280KG |
Size | 650*1050*1950mm | 750*1150*1950mm | 1050*650*1950mm |
Carton Size | 1100*750*1820mm | 1220*850*1820mm | 1100*750*1820mm |
Here is a complete working process of the production line.
FAQ
What’s the process of making a feed pellet?
Crusher→ mixer→ screw conveyor→ extruder→ pneumatic conveyor→ dryer→ bucket conveyor→ counter flow cooler→ roller sprayer→ bucket conveyor→ finished product bin→ packing machine.
How to choose the most suitable fish feed production line?
The machine, the extruder, decides the capacity of the whole fish feed production line. So you can check which model of the extruder is most suitable for you.
What if I don’t want some of them?
Of course, you can choose the machine you need. The machines that are involved in the technological process are for your reference. We can customize the machine combination according to your needs.
I want to know more details about the extruder, conveyor, etc.
Please check this website, there are very detailed articles that introduce each machine on other pages.
Can I change the shape of the pellet?
Yes, of course. You can change the shape of the pellet by changing the molds of the extruder also wealso accept customization.
What’s the warranty time of these fish feed production line machines?
One year.
What floor space do I need to build this equipment?
It depends on what you need exactly. Our sales clerk will help you design the layout according to your plant area, your needed machine, and your budget.
Complete fish feed production line shipped to America
Last week our customer from America ordered this floating fish feed production line. This customer got our contact information from YouTube. And then add our WhatsApp. Through communication, our salesperson fully understands the customer’s needs. And recommend suitable machine combinations to customers. The customer feels that the price of the machine is suitable and finally decides to buy it.
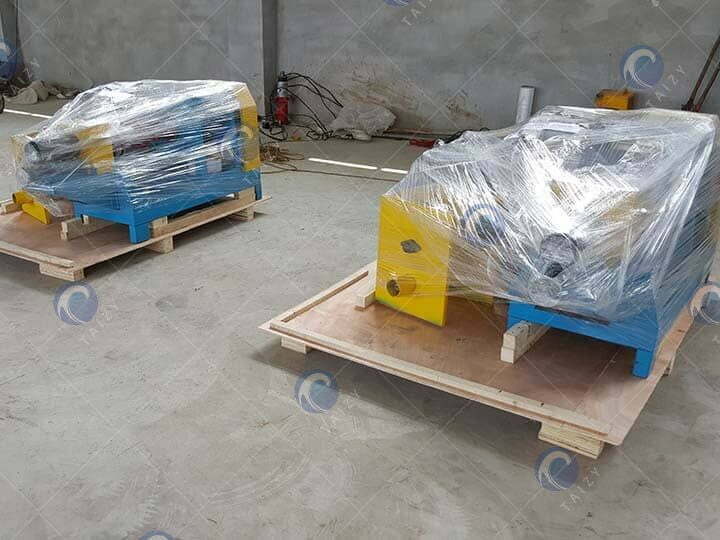
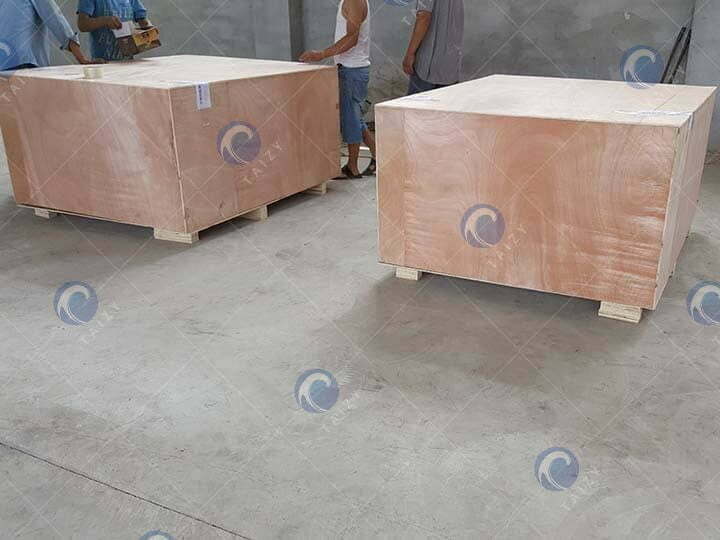
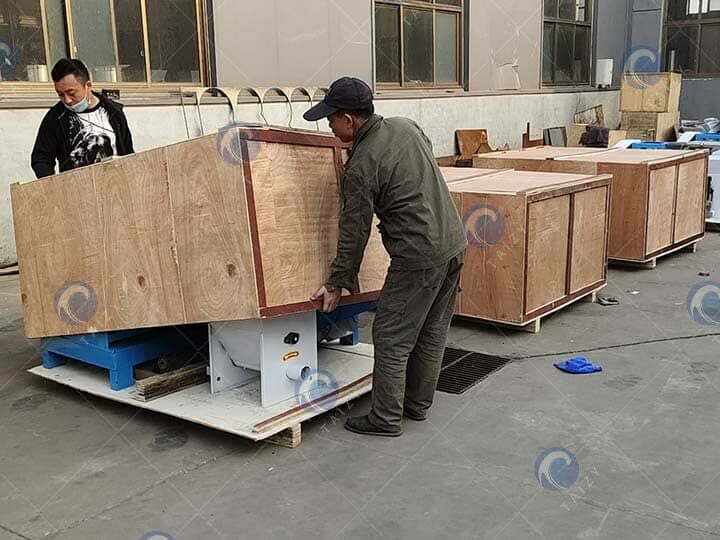
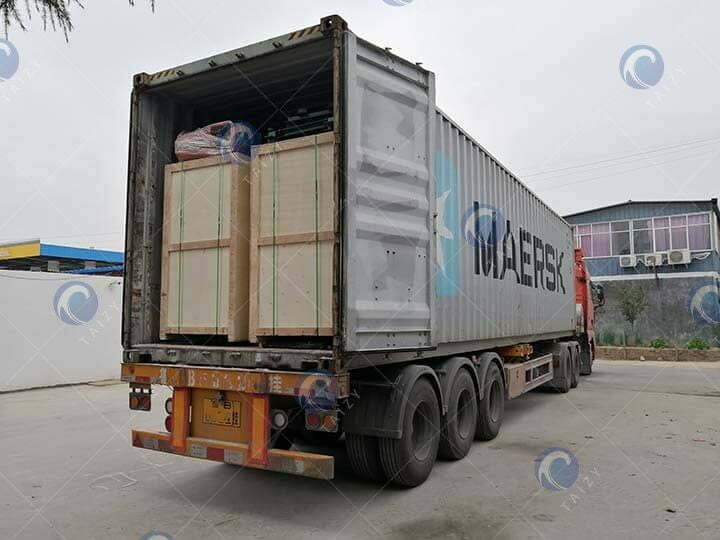